INTERVIEW: Architect Adam Kushner on Building the World’s First 3D-Printed Estate
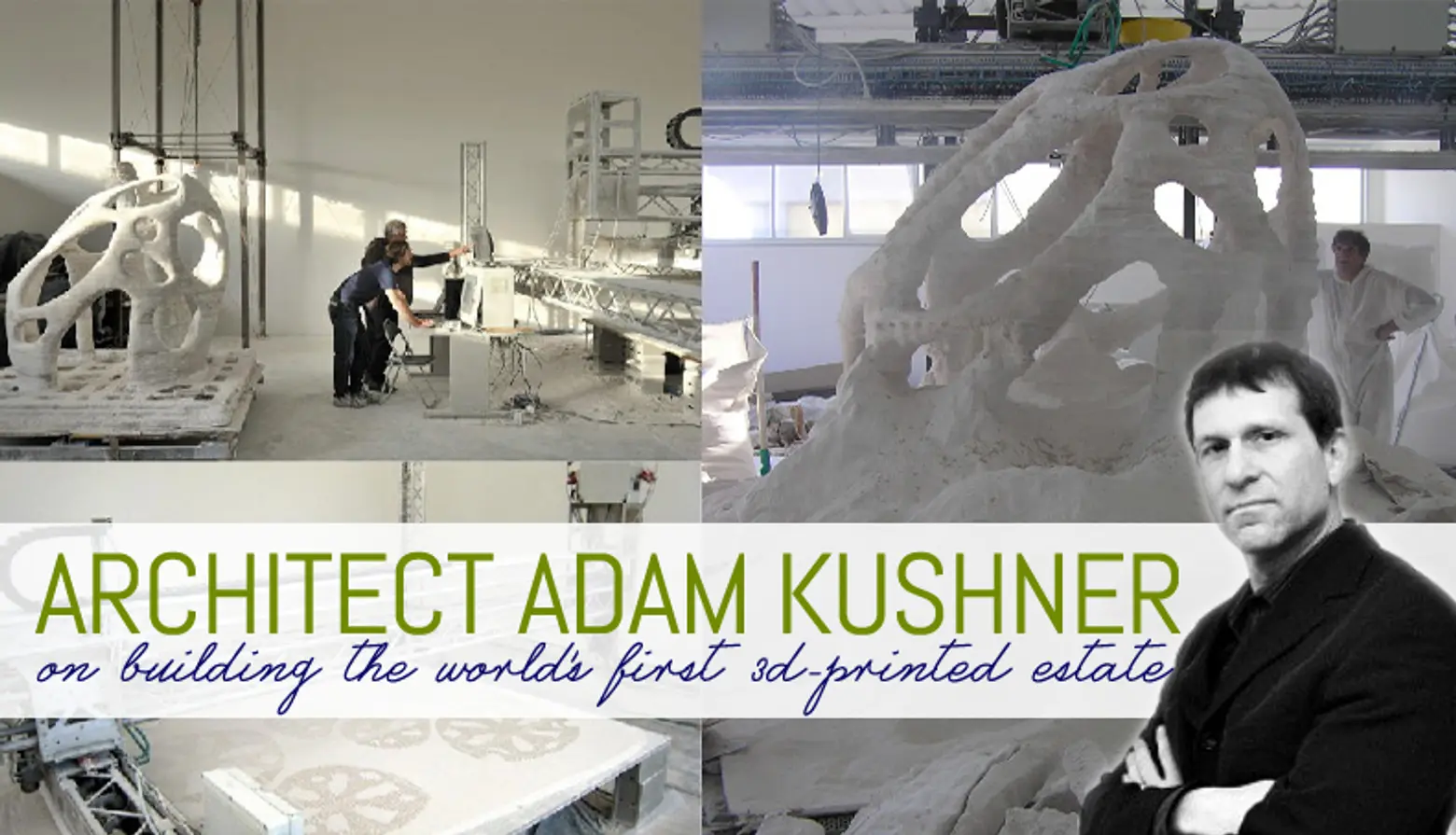
3D printing has been making the design and tech rounds lately, from ceramics and construction bricks to cars and mini castles. But there’s one project in the works that’s looking to blow the rest out of the water. New York City-based architect and contractor Adam Kushner of KUSHNER Studios plans to build the world’s first 3D-printed estate in Gardiner, New York, which will include a pool, pool house, and 2,400-square-foot main house–all of which will be constructed using this new technology.
Kushner has teamed up with Italian inventor and engineer Enrico Dini, who will ship a modified version of his D-Shape printer to New York in January. Dini’s printer uses his patented magnesium-based binding process combined with a material like sand to render stone-like objects. Kushner also teamed up with Enrico’s local contact James Wolff, co-founder of Deep Space Industries, which works with NASA on asteroid prospecting, mining, and processing. The three men, along with Nigel Woods, founded D-Shape Enterprises New York. Adam’s construction company In House Group, Inc. will hire D-Shape Enterprises to build the estate.
Adam Kushner (R) with his electrician while power was being installed at the site
What got you interested in 3-D printing?
I’ve only been exploring 3D printing for about a year and a half, which in a way makes me almost a middle ager in the industry. I read an article about it. I certainly was aware of scalable, small projects, but I read an article on the construction end of it related to Dutch architects being the 3D Print Canal House.
How did you personally get involved with the technology?
I feel that life is a relatively short experience, and we only have a limited time to do certain things. I always made a vow that I would leave this world better than when I arrived in it. When I heard about 3D technology, it seemed like an appropriate sensibility. It touches on scant resources, expensive labor, possibilities of opening frontiers in creativity, and reducing one’s carbon footprint.
Most of the 3D-printed work I was seeing at conferences were accessories and cultural ephemera. I thought, “There’s a better place for this in my world.” I come from a design/build background, and I’m a contractor and have academic pretentions. I’m a designer who builds and a builder who designs. And that’s where I saw my niche.
After reading the article about the Canal House, I assigned Virginia Camillo in my office to go out and see who had done full-scale 3D printing. There are three, excluding the Canal House: Voxeljet in Germany, who does mostly automotive and casting work; Dr. Behrokh Khoshnevis, a professor at UCLA who invented the Contour Crafting technology; and Enrico Dini in Italy, who was the only person to respond to my email. I met him in November 2013 when he was giving a conference in Washington, D.C., and we got along great. I made plans to go to Italy to get a feel for what he was doing. In the interim, he introduced me to his liaison in New York, James Wolff. I then flew to Pisa, Italy in June 2014 and saw the equipment. We formalized the relationship a few weeks later and created D-Shape Enterprises New York.
The D-Shape printer
What made you decide to tackle the world’s first 3-D printed estate?
Because I can; it’s my property, I own it, and I’m the client.
You plan to ship a modified version of Enrico Dini’s oversized D-Shape printer to New York City in January. Can you tell us a little about why you chose this specific printer and how the travel plans are going?
When I was in Italy, I saw three printers. The original goes back seven or eight years. It’s labor intensive and very difficult to keep accurate, but it worked. In Enrico’s factory in Pisa, I saw the second-generation printer, which goes from a salt water/calcium/magnesium composite to a concrete mixture being squeezed through like a pastry bag. And now there’s a third model on the drawing board for our project. It’s modular, scalable, and designed for a container shipment. I’m expecting to get something between the first and second generations. It will still use the salt water system, but will probably be on a three-axis machine with four posts. Its printable area will be 18′ x 18′ x 3’— a size that will fit inside a shipping container. Everything on this project conforms to that as a max size, and then the pieces will be aggregated together. Interestingly, though, the design was in place before I knew limitations of machines.
Pool detail plans
Why did you decide to build the estate in three stages–the pool, pool house, and main house?
We’re starting with the pool because this printer has built artificial reefs commercially and successfully. A pool is in complete compression, so it’s a great first project. We have to prepare the site for the printer’s arrival in January 2015, and within three to four months we’ll start on the pool. We hope to have it finished by the middle to end of next summer. Then we start building the next level of complexity, which is the pool house. That’s where we start dealing with gravity, like roofs. Then we do the third part, the breezeway. It’s all roof and no walls–another layer of complexity. By then I want to cast foundations on soil. We cannot do it today, but the hope is to prepare the soil and then putting the footing in at the same time we’re putting up columns. A year and a half out is building the house, which is a very ambitious, cantilevered structure.
I’m committed financially, programmatically, and I have gotten approvals from the township on the breezeway, pool, and pool house. The pool house is still in the design stages, so has not yet received approval.
Cliffs in the area (L) and the power being run for the building site (R)
How does the Gardiner, New York location factor into the design?
I’m taking cues from the geological strata of the area. I’ve been climbing there since 1985, so I’m intimately aware of the New Paltz area, which is the climbing capital of the northeast. It’s known for the Silurian cliffs. When the ice sheet travelled down from Canada 10,000 years ago, it pushed through the area and formed the Hudson Valley all the way down to the terminus at Long Island. As it retreated back up the Hudson Valley, it formed tightly layered conglomerate rock, and it’s that pattern I wanted to explore.
We took a theoretical line down the center of the property, and we did what’s called a mega transect. It’s a term used in anthropology where you draw a line from two points and look at a cross section. That’s why crushed stone from the site will be used for the pool; we’re using our own resources.
Master site plan
We read that a challenge may be how to plant rebar as the machine pours in the building’s walls and foundation. How are you planning to get around that issue?
Yes, the greatest problem is how to do reinforced concrete, for which there’s no solution yet. There are steel 3D printers and concrete printers, but no one has combined the two. The Chinese have done certain add mixtures like incorporating fiberglass, which gets closer, but it’s still not there. This is also where we hope to find our niche.
Will the 3D-printing process reduce and labor and construction costs?
In theory, you don’t need any labor. I’m assuming it’s a one person job, as opposed to four or five people. One would assume that it would be more cost effective, but I’m fully prepared that any cost savings will be offset by experimentation and do overs.
Estate plan
You, Enrico Dini, and James Wolff created D-Shape Enterprises New York. Do you plan to create more 3-D printed homes after this one?
Yes! I’m assuming the minute we get the pool out, we’ll have a pool business. And the same with the Jacuzzi and the fountain. There’s a great skepticism in the industry. This is the Wild West, and we’re leading the charge; it’s the great land giveaway and we are all running into the open desert not knowing where to stop.
There is currently no industry standards, but we have more integrity than to charge what we want. This is to try to make the world a little better, but we’ll make some money doing it, too. It’s one thing to build in an upstate hamlet, but it’s another to build in Manhattan. That’s the next goal.
How is construction progressing?
Power went live last month. The next step is meeting the excavator and putting the foundations in during these next two months before weather turns. That’s being done old school with poured concrete. We’re currently working on the STL files, which are the same type of file used for desktop 3D printers. We then plan to print a small-scale model of the estate.
***
[This interview has been edited]
KUSHNER Studios
In House Group, Inc.
Images courtesy of KUSHNER Studios and D-Shape