Where I Work: Go inside SHoP Architects’ aviation-inspired offices in the Woolworth Building
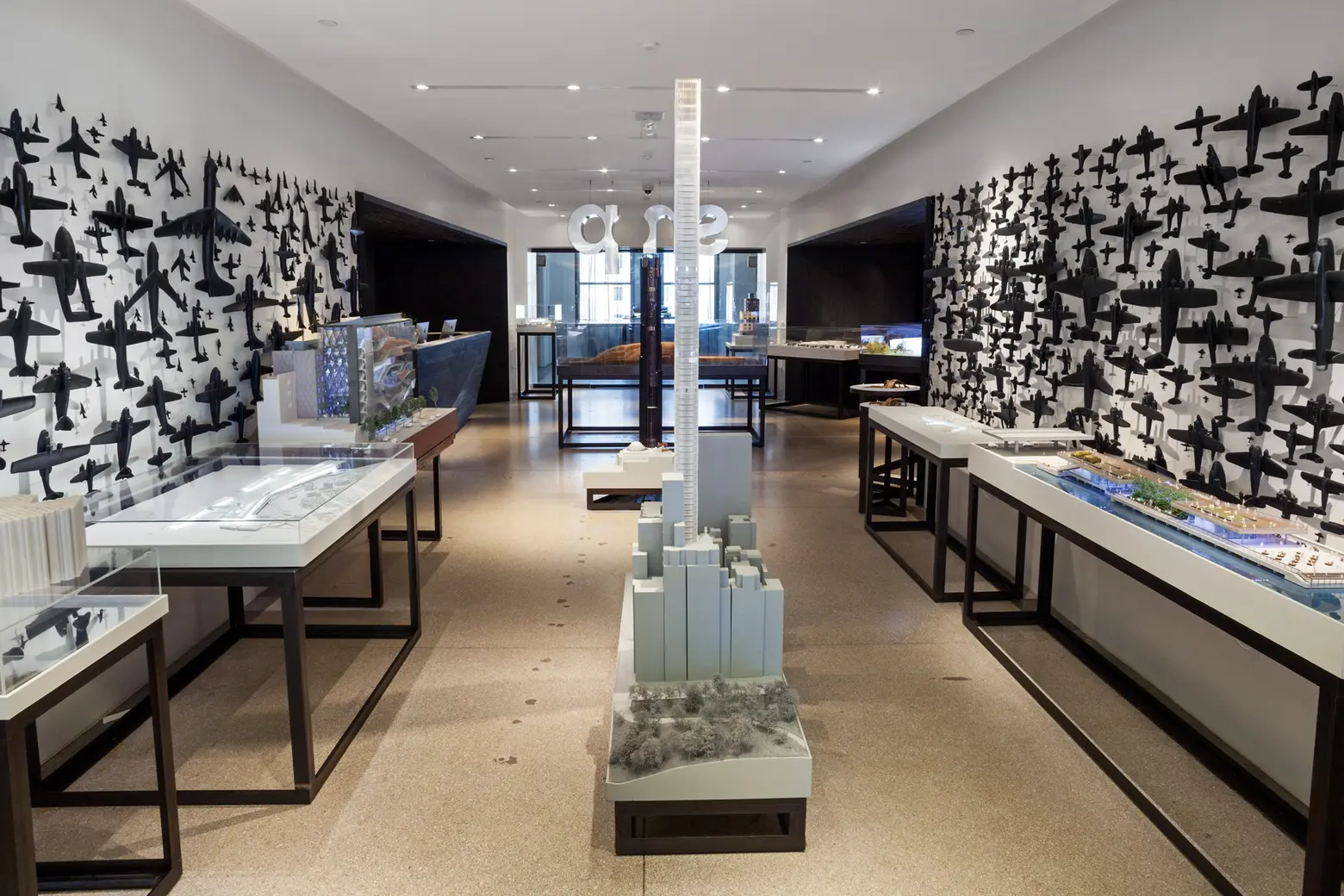
6sqft’s series “Where I Work” takes us into the studios, offices, and businesses of New Yorkers across the city. In this installment, we’re touring the Financial District offices of SHoP Architects. Want to see your business featured here? Get in touch!
The largest collection of WWII-era spotter planes in the world, a massive copper section of the Barclays Center facade, a materials library with hundreds of samples of everything from fabric to flooring–these are just some of the surprises you’ll come across in SHoP Architects‘ offices in the iconic Woolworth Building. The firm’s projects include buildings at mega-developments like the Domino Sugar Factory and Essex Crossing, the twisting American Copper Buildings, and the world’s future tallest residential skyscraper 111 West 57th Street, and their office certainly embodies this creativity and range of work.
After taking a tour of the space, 6sqft chatted with Associate Principal Angelica T. Baccon about this very special office design, what a typical day is like at the firm, and, of course, the backstory behind those planes. We also met with Materials Librarian Kate Smith to learn a bit more about this rare resource that helps inform the ideas at SHoP.
In the lobby, a model of Dunescape, the 2000 winner of MoMA PS1’s Young Architects Program competition
L: A model of a proposed master plan for LaGuardia Airport (Bill and Chris, naturally, love airports, too!); R: A model of Pier 15 on the East River waterfront
The model on the right shows SHoP’s design for a new academic building for FIT
Angelica, tell us a bit about Bill and Chris’ passion for planes.
The collection that you see on the walls of our office is the largest single collection of WWII-era spotter planes [in the world] – even larger than that of the Smithsonian. Bill and Chris grew up in a family fascinated with planes, boats, and cars and have carried that passion with them since childhood. Their collection has also become a metaphor for SHoP’s work – we focus on the idea that each design must serve a specific purpose, much like the design of each plane dictates its unique functionality.
Miniature plane collections in the offices of SHoP partners and brothers Bill and Chris Sharples. The phone booth rooms are named after various plane parts.
What made SHoP decide to incorporate planes into the office design?
It is a reminder of our roots. Much of SHoP’s early work is inspired not just by airplanes but model planes specifically – they are delivered to you as a kit of parts, and each piece fits together to make the whole. We approach architecture in a similar way.
The reception area is lined with publication covers in which SHoP was featured
SHoP renovated their office space four years ago. Can you tell us a bit about this process?
Because we are very data-driven, we did a lot of surveys and analysis on what the needs and wants were at our workspace and how this impacted our workflow. Pinup space at the time was in high demand, which is why you see felt everywhere. Storage was also a very big deal; if you had been to our last office, you would know why! We incorporated a lot of storage space within the project bunks, shelving, and closets.
The idea of having a central space where the whole office could come together was key. The U shape of the Woolworth building itself played into the design and inspired the way we are currently arranged. The “Equator,” as we like to call it, was envisioned as an active, multipurpose, loud, always-changing space. It was naturally positioned at the center of the U. Once that was located, everything else fell nicely in place.
Even though the space works well now, our workflow has evolved since we moved in. This has allowed us to really put the office flexibility to the test. Things like incorporating VR into our daily workflow or having the opportunity to communicate online with international clients have really forced us to explore space for the “digital.” The Equator has been incredibly resilient and now hosts anything from VR stations to floating digital screens.
The conference rooms are named after types of planes
Is there anything you wish you could change about the office?
Recently, we’ve been doing a lot of coworking analysis, studying how offices expand and contract, and how static floorplates have the potential to adapt. Connectivity is a driving force of these studies. It would be interesting to see how a bridge connecting the open part of our “U” floorplate would impact our workflow.
A display of 3D-printed models. On the left of the top shelf are four iterations of 111 West 57th Street. The piece on the wall is a scale display of all the components it took to make one of SHoP’s first projects, Camera Obscura.
Do you have a favorite part of the office?
The hallway that connects the two wings. Functionally, it serves as a hallway, but this spine has organically hosted a variety of programs. People gather there and pin up work, have team conversations, client presentations. It’s not a stagnant space; it’s always active and contributes to our workflow.
In the common space, the Woolworth Building’s original Terrazzo flooring and steel columns remain.
Speaking of, the common areas seem well utilized. It must be a collaborative environment?
When we first moved in, we thought the Equator was going to be more of a hangout space, and it’s morphed into a place where teams actually work! Everyone has taken this flexible space and made it their own. Of course, people still socialize there, but they also have informal meetings, or host talks and volunteer activities. It’s also the space with the best light, so we do a lot of our model shots there, and we also bring materials out into that space to see how they look in that light to help us choose colors and finishes. It has definitely surpassed our expectations of multipurpose.
Even the way the facade piece is lit is the same as those on the actual Barclays Center
We love that you have a piece of the Barclays Center facade here–how did this come to be?
When the two modular towers next to the arena started going up, we had the opportunity to reclaim a couple of the Barclays panels for our office. Because a lot of our projects are really about materials and how they look and feel and come into contact with people, we thought it would be a fantastic opportunity to have a piece of this façade to showcase.
The mini fabrication lab
What types of technology is the firm using to make their models?
There are so many great technologies out there now that provide a variety of different outputs. We are using anything our teams can get their hands on, from innovative 3D printing technologies (we recently collaborated with BRANCH on a 3D printed structure) to more analog tools (we also know how to weld!). It’s all about knowing how to use the tool to create the model or effect that you’re after. Models are great tools for communication both internally and externally, so we never limit our tool kit and we are always open to learning how to use new tools both physically and digitally.
Outside the elevators on SHoP’s floor of the Woolworth Building. No photography is allowed in the building lobby, but these elevators show the Art Deco details.
It must be incredible working in the Woolworth Building!
Yes, it’s amazing! It is really inspiring to walk into the building and think that this was one of New York’s first skyscrapers, but I think that its location, central to so much of the city, is the best thing about it. It’s close to City Hall, to a lot of projects we’re working on, you can walk across the street and there’s City Planning. It feels like it’s very connected and integrated into the city.
The entrance to the Materials Library features an actual piece of the Nassau Coliseum facade
Kate, can you give us some background on the function of SHoP’s Materials Library?
The Materials Library is involved in almost every project at SHoP. It houses new samples from vendors, control samples for our projects, and records of materials used on previous projects. Day to day, we source new and interesting materials for upcoming projects. We advise on materials that would be appropriate for exterior and interior use. We put together furniture packages for our exciting new amenity-focused projects. We also help coordinate projects that are in construction by acting as a connection with our vendors. Our vendors help make sure things are happening on time and that product is in stock. Every day designers come into the library looking for inspiration and solutions to design questions.
It’s such an interesting role you have–what is your background?
I received a Bachelor of Arts in Art History from Colorado College. While I was in school, I worked in collections and curation at the Colorado Springs Fine Arts Center. I also took architecture classes focused on the major designers and architects of the 20th century. After I graduated, I worked at the Denver Art Museum in collections for a few years before moving to New York. My experience in organizing and keeping track of the thousands of objects in the Museum collection has translated to managing and organizing the materials at SHoP.
Do you have a favorite material or fabric?
I think my favorite material is velvet – it’s making a total comeback! I love a plush, thick velvet in jewel tones or a pop of mustard yellow. It brings a softness to our palettes but can be mixed with other materials like leather and big graphic fabrics to keep our designs fresh and fun.
SHoP is known for its direct-to-fabrication design, which they pioneered with the Barclays Center facade. The Stagg Street fabrication lab boasts a CNC cutting machine and a Kuka industrial robot. Photos of the fabrication lab via SHoP Architects
Angelica, what about the fabrication lab in Williamsburg–what types of projects go on here?
Our fabrication lab at Stagg Street offers a platform for us to be able to augment our model-making at a different scale. It’s a place where we can experiment and build out large-scale models or portions of projects. The bigger or finer the detail of the model, the better we can represent it in our sets, but also have the client experience it firsthand.
+++
RELATED:
- Where I Work: Tour FXCollaborative’s Flatiron architecture office with partner Dan Kaplan
- Where I Work: Architecture firm Woods Bagot shows off their ‘raw’ FiDi studio
- How COOKFOX Architects outfitted their Midtown office with wellness technology and outdoor space
All photos taken by James and Karla Murray exclusively for 6sqft unless otherwise noted. Photos are not to be reproduced without written permission from 6sqft.
Fabrication Lab photos by SHoP Architects